
Carnival Glass - A Concise Guide


SECTION 4:
A RE-EMERGENCE - CONTEMPORARY CARNIVAL GLASS
In the early 1930s volume production of decorative Carnival Glass virtually ceased in the USA and Western Europe. The impact of the 1929 US Wall Street Crash and the resulting Great Economic Depression cannot be overstated.
Millions of working-class Americans who had been the enthusiastic purchasers of decorative glass no longer had cash to waste on frivolous home furnishings.
The market for it disappeared affecting home production and imported goods. Glassware became simple and practical: the so-called depression glass and any iridescence was machine applied as a colour flashing.

Popular taste had also moved on to favour the new Art Deco style with its simple clean lines, often geometrical and with little detailed ornamentation.
​
In the US this was manifested as Stretch glass, still iridised but without patterning, and often elaborately hand shaped and finished.
(Photograph of a Lancaster Glass ruby lustre stretch lidded comport with applied decoration is courtesy the American Stretch Glass Society)
In the UK and Europe, Art Deco glass was not iridised but incorporated new glass formulations and treatments such as cloud, opaque and acid etched finishes. Much of the Art Deco glass was high quality, relatively expensive to buy and directed to the remaining more affluent sector of customers.
The final blow for all decorative glass production was WW2 coming at the end of the 1930s. This effectively curtailed and disrupted the industry until the early 1950s, by which time Prime Carnival Glass was decidedly an old-time product largely overlooked by the current generation.
Some Carnival Glass was still made in this period. In the UK, Sowerby, returning to decorative glass production, reintroduced Carnival Glass, pressed and iridised traditionally by hand using their pre-war moulds.
This included some from the 1930s not previously made in Carnival, such as the Hen and late version Swan butter dishes.
In the US, firms including Anchor Hocking and Jeannette, produced lines of iridised patterned glass on modern fully mechanised production equipment. (Anchor Hocking Swirl Pattern tea set in peach lustre courtesy Dave Richards).
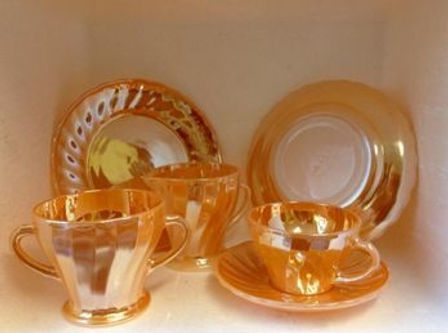
In Germany, companies like newly formed VEB Sachsenglas made items for export often using moulds from their predecessor, Walther & Sohne.
The revival of interest in Carnival Glass as a prime collectable, can be traced to the early 1950s when a group of influential American collectors began to document and disseminate information about it. These included pioneer collectors such as Gertrude Conboy, Marion Hartung, Rose Presznick and Don Moore. Their research and writings fuelled interest and led to the formation of dedicated Carnival Collectors Clubs. Although this movement was concentrated on the original Carnival Glass from earlier in the century, the raised profile and demand for the glass stimulated firms such as Fenton and Imperial, to start making it again in the 1960s, initially by reviving old moulds which were already in their possession but going on to produce new mould designs through the 1970s, 80s and beyond. This output would become known as Contemporary Carnival.

Other glassmakers including Indiana, Levay, Moser, Boyd, Summit, L. G. Wright and Westmoreland all entered the market. Carnival Glass was made in new colours and a wide range of forms not seen in its original classic period.
Many of the new designs were created as club souvenirs or as novelties such as this Fenton ice blue butterfly (photograph courtesy S&T Auty).
There was also a trend to reuse old original moulds to create new items in this period which often caused confusion with the original pressings, much to the consternation of collectors. Fenton produced the largest range of Contemporary Carnival for the longest period, being the last of the larger US producers to make it until they finally went out of business in 2016. It is still made in very limited quantities by smaller US glassmakers such as Moser.
Iridised glass, however, will always hold a unique fascination as a bright attractive home decoration. At one end of the scale, the iridising process is often used by Art Glass producers to enhance very expensive hand blown patterned and textured glass, and at the other, supermarket home furnishing shelves carry inexpensive lines of iridised patterned vases, bowls, trinket boxes, glasses and candle holders such as these examples made in India (in dark and pale marigold with a hexagon pattern) and China (central tea light in clear white iridised glass), photograph courtesy S&T Auty.

Don’t forget to read Section 5: Carnival Glass - What’s in a Name?